How Injection Molders Maintain Clean Room Standards (and the Importance of MedAccred Accreditation)
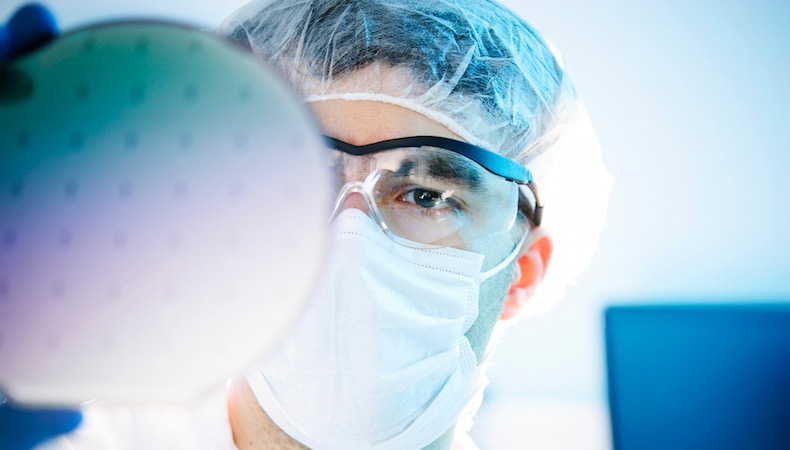
Complex medical applications require devices and equipment that are protected from dust, chemical vapors, aerosol particles, airborne microbes, and other contaminants that could compromise product quality, integrity, and safety.
Responsible injection molders providing services to medical manufacturers are obligated to adhere to stringent protocols. Beyond operating in clean rooms that are ISO 13485:2016-certified and 21 CFR 820-compliant (the prevailing standards for ongoing quality), MedAccred accreditation assures medical OEMs of an unparalleled benchmark of production and quality standards.
WHAT IS MEDACCRED?
MedAccred, managed by the Performance Review Institute, is a medical device supply chain oversight program with a top priority of reducing risk to patient safety. This is done by verifying compliance with critical manufacturing processes and improving the quality and consistency of medical devices. Earning accreditation is a rigorous process, and few injection molders (including Kaysun) have been awarded the distinction.
Clean Room Classifications
In addition to ISO and CFR standards, clean room injection molding environments are classified, typically into ISO 7 or ISO 8. Certification for the former verifies that the clean room contains 10,000 pollution particles per cubic foot, and the latter means the clean room is certified to 100,000 pollution particles per cubic foot. The type of clean room used for manufacturing is dictated by specific product and/or customer requirements.
Clean Room Considerations
Maintaining and regulating clean room protocol and, by extension, clean room certification and accreditation for medical injection molding are comprehensive. Clean room injection molders must pay strict attention to a number of variables in order to remain in compliance, including:
- Quality control systems, such as HEPA filters and machine hoods, that monitor, manage, and remove particulates and dust that could otherwise cause the requisite number of pollution particles to fall out of specification for ISO 7 and ISO 8 clean room standards.
- Procedure documentation that physically traces the process lifecycle, mold pull cycles, and equipment/product testing so verification of controlled conditions are readily available in the event of repeated cycles, routine check, customer request, or procedural deviation.
- Work environment controls that test air quality for purity and routine, comprehensive equipment checks to find and address contaminants that result from production — like particulates from ejected parts, peeled or shaved undercuts, and microscopic plastic parts. Further, machine maintenance can introduce contaminants if not done properly. Over-greasing components, for example, can be particularly detrimental.
- Risk management through implementing specific analysis modules like fault tree analysis (FTA), failure mode and effect analysis (FEMA), and hazard analysis and critical control point (HACCP). Knowing and evaluating the microbial risks helps injection molders identify acceptable limits and develop consistent contamination control assessments during manufacturing.
- Requirements traceability for FDA-regulated implantable medical products that are intended to remain in the human body in excess of one year, non-implanted, life-supporting devices used outside of medical facilities, and all other complex applications whose failure would also likely have serious, adverse health consequences.
- Machine operators must fully commit to the procedures within a clean room, as cutting corners is unacceptable. Plus, they must strictly adhere to wearing protective gear like gloves, gowns, masks and booties to protect clean room environments and the injection molded parts and components from contamination.
The ability to adhere to clean room practices, certifications, and MedAccred accreditation standards is only one benefit of partnering with an experienced, ISO-certified clean room injection molder. Find out more about specialized engineering and how to produce repeatable, defect-free injection molded components in our white paper, The Importance of Scientific Molding in Medical Device Manufacturing. Click the button below to download your free copy.
Subscribe
TO OUR BLOG
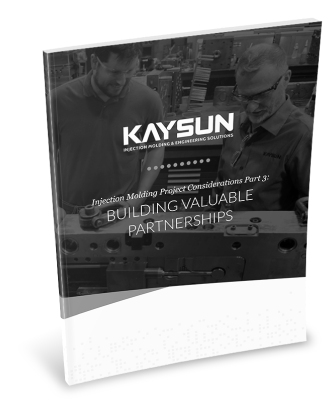
How Do Injection Molder Partnerships Influence Project Costs?
You Might Also Like...
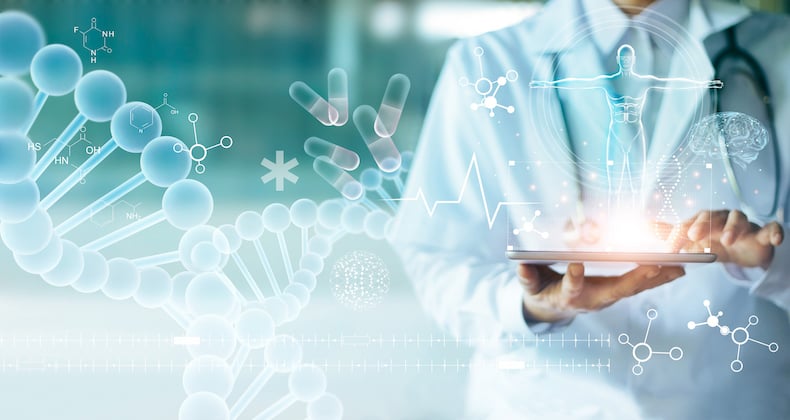
How MD&M West 2024 Keeps MedTech Professionals Ahead of the Curve
MD&M West is one of the largest and most respected medical device trade shows …
READ MORE

How MedAccred Accreditation Helped Kaysun Enhance Processes & Quality Systems
When you operate at the top of your game, reach higher. Kaysun had already shown i…
READ MORE
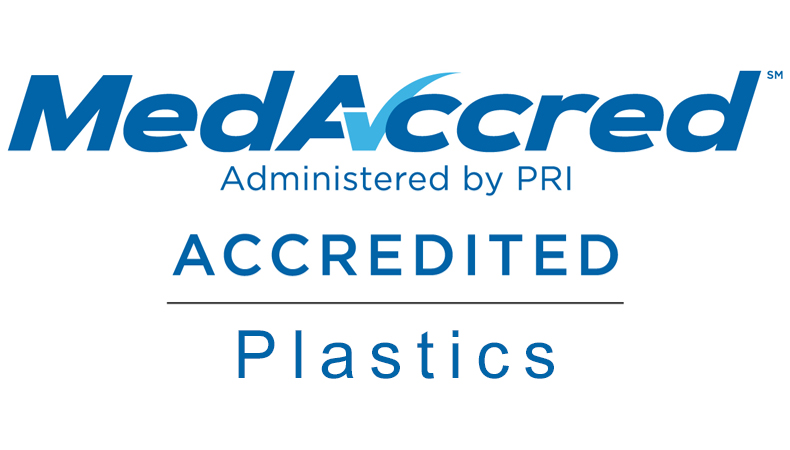
Why Ongoing MedAccred Accreditation Matters to Medical Manufacturers
Kaysun's commitment to excellence is well documented through its certifications, i…
READ MORE