Plastic Regrind Saves Injection Molding Materials and Money
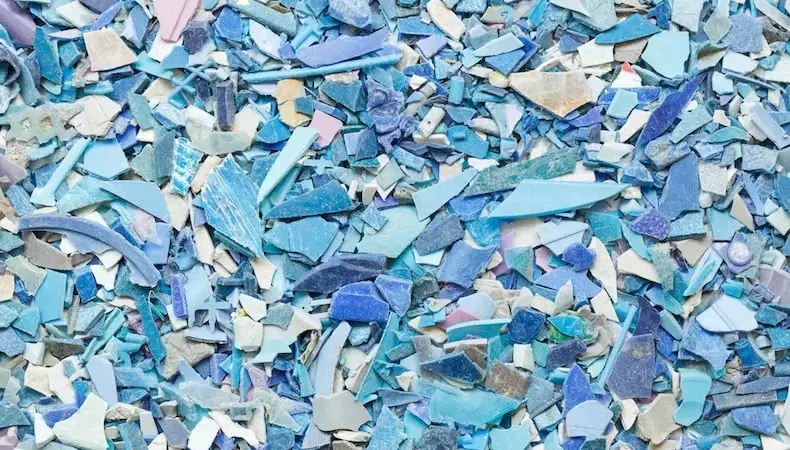
Controlling costs is a huge part of any project. Materials can be expensive, especially advanced or specially engineered resins, so you want to select the right plastic and get as much bang for your materials buck as you can. One way to do this is the proper use of plastic regrind.
There's often some unused thermoplastic material that's left over from injection molding, such as scrap parts, runners, and sprues. Why waste it?
Even though this material has been processed once, it can be used again (within certain guidelines). This excess material is collected and ground into much smaller granules called plastic “regrind.”
Most material manufacturers agree that up to 30% of compatible regrind material can be mixed in with virgin material and not lessen or compromise the mechanical properties this primary material is supposed to have. Further, including 30% regrind material translates to a roughly 15% cost savings — just one of the many advantages.
WHAT IS REGRIND? WHAT ARE ITS Benefits?
Using plastic regrind is a great way to reduce cost, optimize material usage, and reduce demand on natural resources. These are all great benefits, but they come with a word of caution: Regrind is not ideal for highly critical applications. The precision and specificity of these types of projects cannot tolerate the slight variability that regrind material introduces.
Like everything else about injection molding, mixing in regrind is a science that requires high accuracy.
The amount of plastic regrind that can be used, and how it may impact the characteristics of primary material, varies from project to project — variables include resin type, how the regrind was originally processed, granule size of the regrind, and any contamination on the regrind material such as dirt, dust, water, etc.
It's critical to fully understand to what degree the heat history and processing of the regrind has degraded its physical, chemical, and flow behavior, and how much these changed properties may affect these same properties of the primary melt when the regrind is added. Plastic regrind will never behave exactly the same way as virgin resin. How much regrind can be used depends on the performance specifications of the final product and the tolerances that are required.
Important Considerations FOR PLASTIC Regrind
Degradation
The level of degradation for most polymers during injection molding is well known and, for the most part, degradation in the regrind does not negatively impact the quality of the virgin resin if regrind is kept to 30% or less of the melt.
The biggest cause of degradation is heat — it's important not to overheat the material during processing or subject it to too much shear. If the heat history of plastic regrind is overlooked, it's possible that products made from a regrind blend could fail in the field. The injection-molding process may also result in shorter polymer chains in the regrind, which can greatly impact quality and performance.
Granule Dimensions
During regrind, leftover plastic (including tiny dust-like granules and any rejected parts) is collected and passed through a grinder, which reduces the range of sizes from dust-sized to up to half an inch.
While these granules ultimately won't melt at the same rate and there will be some variations in the molded part, these are typically not serious enough flaws to impact quality or performance. This uneven melt rate can be more of a problem for products where aesthetics are important because regrind can cause tiny surface blemishes or discolorations.
Outside Contamination
Of course, clean material handling and clean operations are essential for every plastic injection molding project. All plastics (including regrind) must be free of dust, dirt, oil from the skin, or foreign particulates such as metal or plastic residue from other products. Moisture is a big issue too — if regrind is not properly dried, its physical properties can change significantly during injection molding, which compromises the quality and performance of the final product.
Controlled use of regrind materials is a key component in reducing overall cost. When the same percentage of regrind can be used for a product line, the process can be modified to always accept this blend ratio. However, if the percentage changes, the injection molding process needs to be adjusted accordingly.
Implementing plastic regrind is one way to run an environmentally responsible business that, like Kaysun, is focused on reducing landfill waste.
For an overview of the versatility and value of high-temperature plastics, download our white paper on High-Temperature and High-Performance Plastics.
Subscribe
TO OUR BLOG
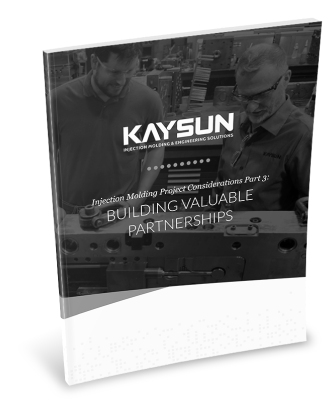
How Do Injection Molder Partnerships Influence Project Costs?
You Might Also Like...
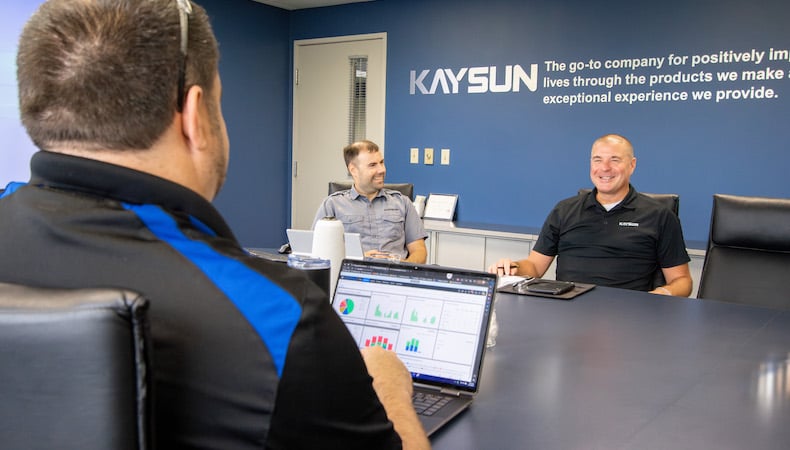
Top 3 Custom Injection Molding Trends to Watch in 2025
Despite being considered more energy efficient and producing less waste than other…
READ MORE
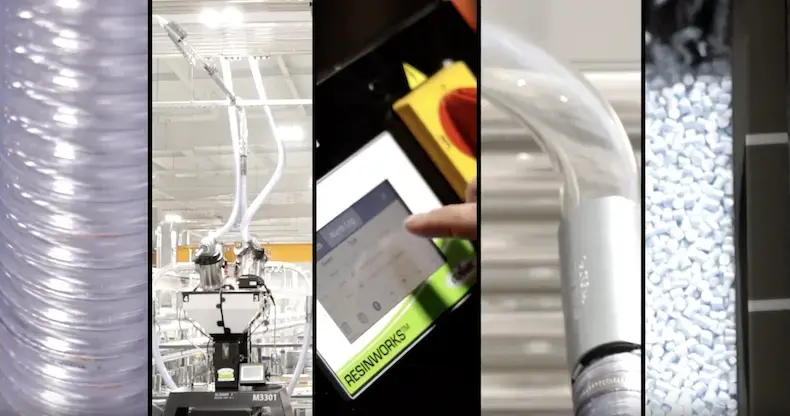
How Centralized Material Handling Streamlines Injection Molding
We consistently look for new ways to deliver timely service and top-quality parts …
READ MORE
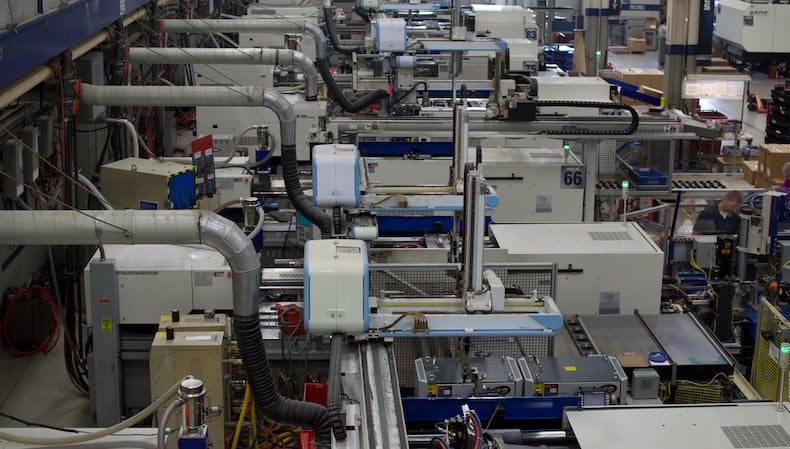
Top 14 Benefits of Injection Molding
OEMs across many industries enjoy the benefits of injection molding. It’s ideal fo…
READ MORE