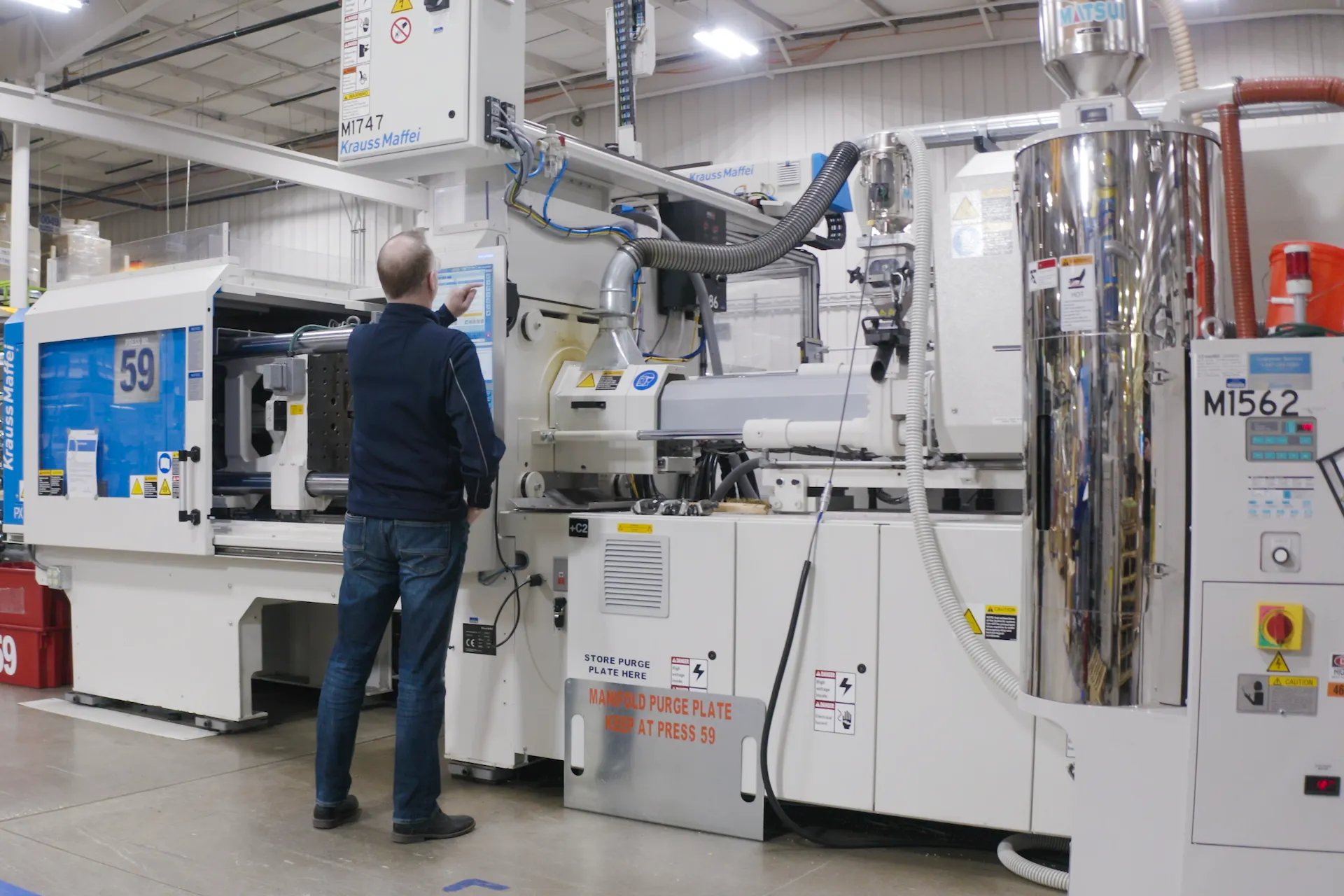
Scientific Molding
What is Scientific Injection Molding?
Scientific molding is a systematic approach to injection molding that’s based largely on the tenets of the scientific method (developing and testing a hypothesis, drawing conclusions, and providing reproducible results). It uses comprehensive data collection and analysis techniques to develop and document the specifications, settings, and steps required to create a tightly controlled and repeatable manufacturing process.
Traditionally, components are brought into specification using a “trial and error” molding process. Scientific molding eliminates the guesswork and rework by using advanced sensors and sophisticated software to establish melt and cooling temperatures, fill rates, pack and hold pressures, and other material-specific variables prior to production. Similar technology and benchmarking is used to monitor each phase of the molding process to ensure consistent quality, precision, and defect-free repeatability.
The Benefits of DfM Analysis
The value of DfM analysis lies in the focus placed on finding practical solutions to project impediments that could jeopardize successful outcomes. DfM analysis defines opportunities for reducing costs, improving manufacturability, and increasing speed to market.
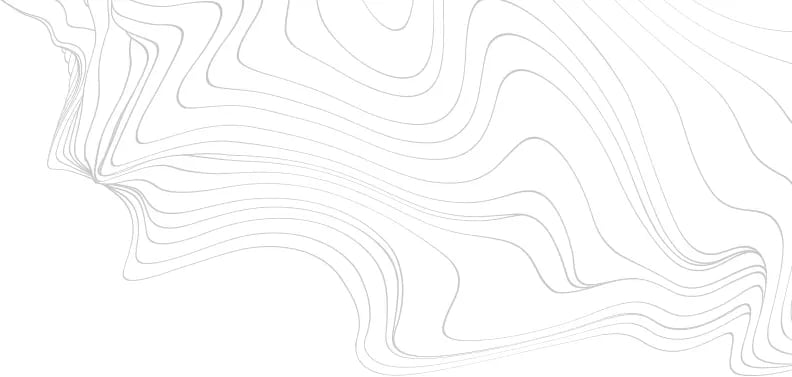
Benefits of Scientific Molding
The robust process established by scientific molding — specifically the data captured and recorded during the process — translates to consistent, repeatable high-quality outcomes throughout all production cycles with minimal setup, regardless of when or on which machine the runs are completed.
Scientific molding provides significantly improved process control over traditional molding methods, which saves OEMs significant amounts of time, money, and materials.
Repeatability, process validation, and meeting compliance requirements are easily achieved with scientific molding, which is a boon for highly regulated industries, such as medical markets.
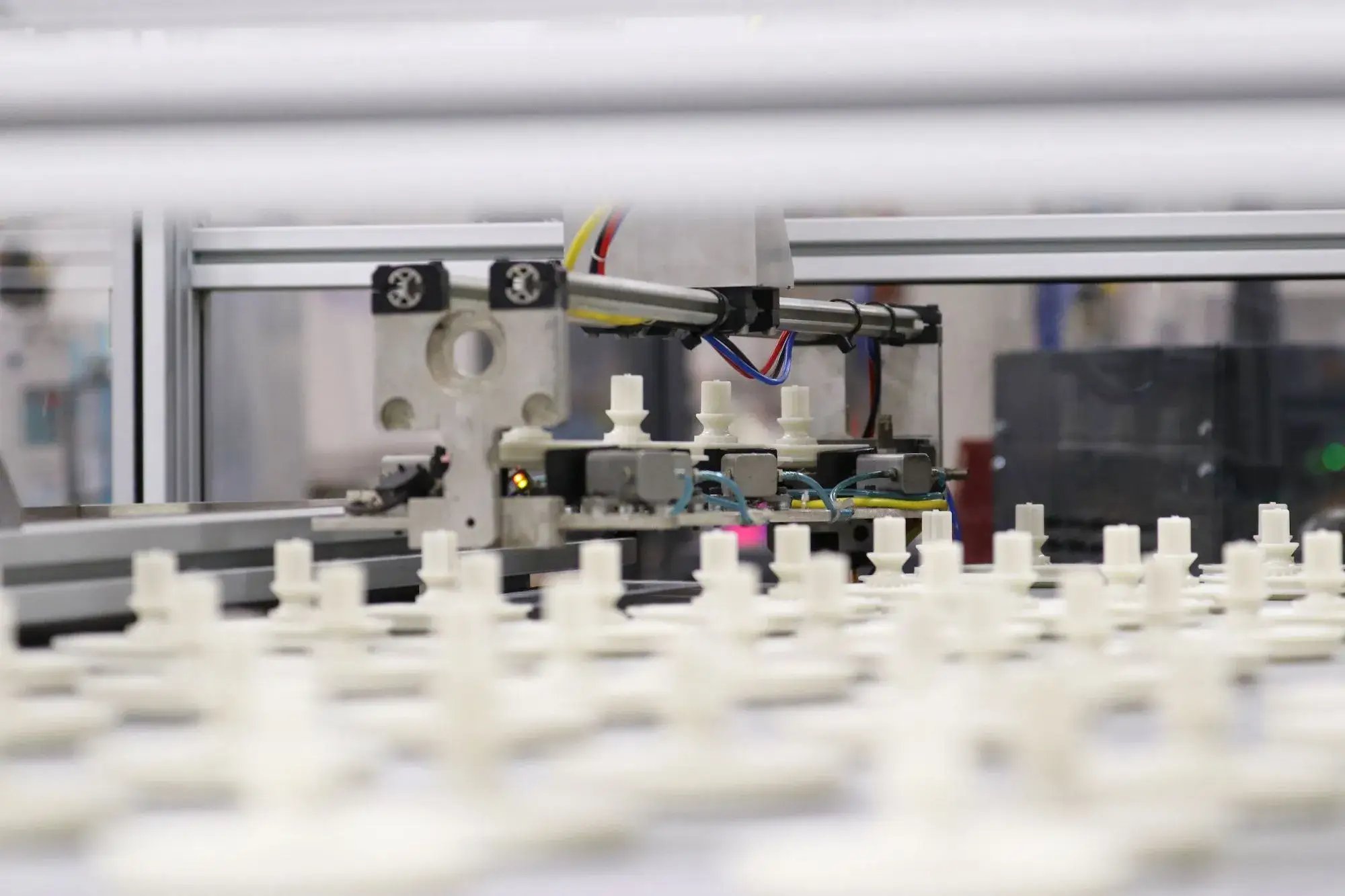
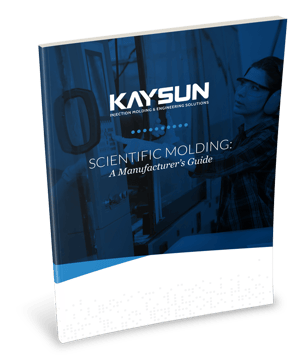
AN OEM'S GUIDE TO Scientific Molding
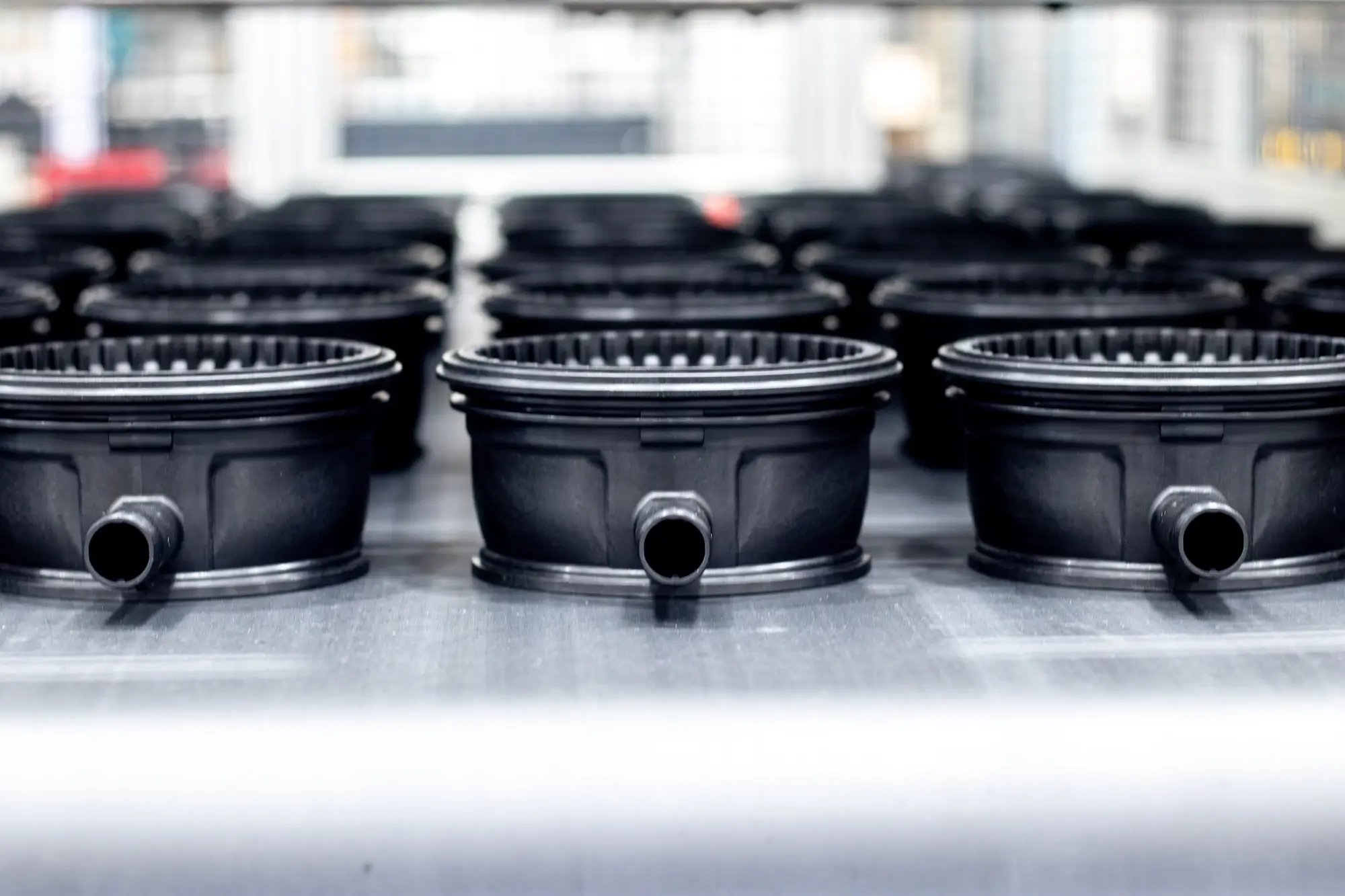
Steps in the Scientific Molding Process
While unique to each application to which it is administered, the scientific molding process can be broken down into six essential steps used by highly specialized engineers:

STEP 1:
REVIEW AND RECOMMEND
Upon review of the initial part design and its complexity, the molder recommends the implementation of scientific molding, if appropriate, to the OEM.

STEP 2:
DESIGN PART AND TOOLING
Both the plastic part and the tool must be designed by specially trained engineers to accommodate scientific molding sensors.

STEP 3:
BUILD TOOL
The first iteration of the tool is constructed based upon initial design specifications.

STEP 4:
ESTABLISH PROCESS WINDOW
Testing the tool is at the heart of scientific molding. Specially trained engineers hypothesize and conduct a Design of Experiments (DoE) to test variables and establish the process window – the parameters that must be consistently applied in production to produce optimal injection molding

STEP 5:
MOVE TO PRODUCTION AND MONITOR
Once the process window is established, full scale production may begin. The process window is closely monitored and remains consistent throughout production.

STEP 6:
MAINTAIN
Proper tooling and machine maintenance (cleaning surfaces and sensors, etc.), ensures adjustments are minimal and is critical to preventing downtime or defective parts across product runs.
Learn More About Each Step
Applying Scientific
Molding Expertise
Process and production engineers use the following to ensure quality testing and monitoring parameters are established, documented, and meticulously followed:
Helps determine the optimal viscosity and injection speed, making it a crucial part of the scientific molding process.
Helps identify the fastest fill rate that can be used without causing flash or other aesthetic flaws.
Shows the actual pressure inside the tool, capturing the material’s behavior when it can’t be detected by the human eye. This is really the core of scientific molding. Specialized training allows the engineer to visualize what’s happening to the plastic inside of the tool.
Combined with injection speed, pressure, and fill time to help the engineer determine the optimal mold parameters. Once these parameters are recorded as the template, it can be used to replicate the process across different machines.
Used when setting up the process parameters and troubleshooting process issues. It allows engineers to make simultaneous adjustments to the variables — a significant efficiency versus earlier traditional “guesswork” troubleshooting methods.
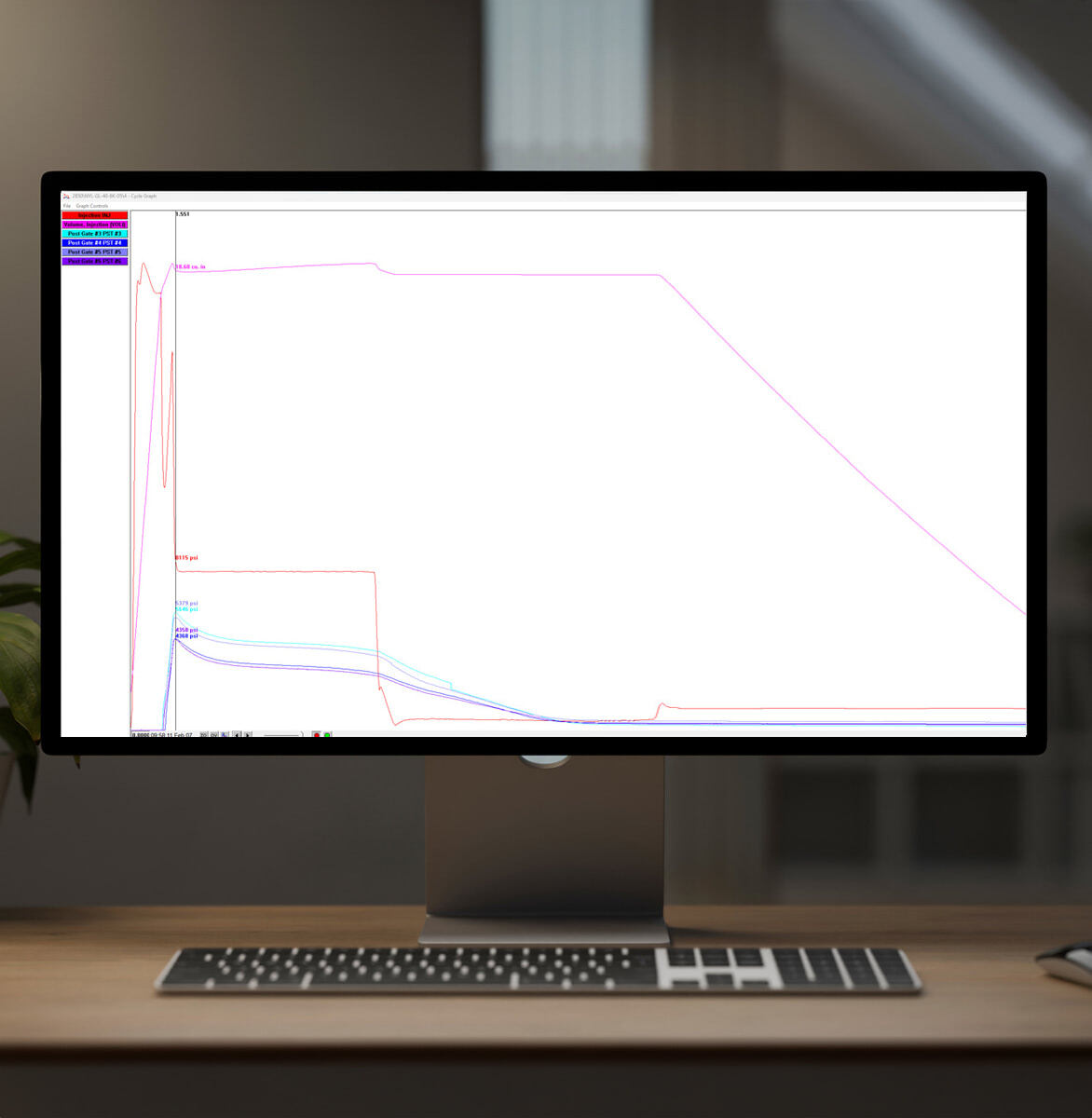
Why Scientific Molding
Requires Specialized
Engineers
Scientific molding is a powerful process, partially because of the specialized engineers who’ve undergone thorough training and earned the proper levels of scientific molding certifications.
RJG, Inc., a leading injection molding, training, technology, and consulting company, has played an important role in developing injection molding professionals for nearly 40 years. Their certifications have long been the benchmark for excellence in injection molding.
Kaysun’s scientific molding specialists, for example, hold RJG-designated certifications in Systematic Molding, and RJG Master Molder® I and II. The master molder programs center around scientific molding best practices, with key focus areas in plastic behavior, process development, and data-driven molding process optimization.
These highly trained scientific molding engineers oversee key phases of each project — specifically tool qualification and production — but it’s more than just using specialized injection molding sensors and software; it’s about knowing exactly what to do to optimize the production process.
That level of knowledge requires a clear understanding of what’s happening inside the tool. The engineers must be adept at interpreting data in order to identify and address any process template deviations, and/or to efficiently set up an existing tool for a new production run or on a different machine.
Above all, scientific molding engineers are problem solvers who are aided by software in finding and fixing process issues, and providing solutions that will quickly return the process to specification.
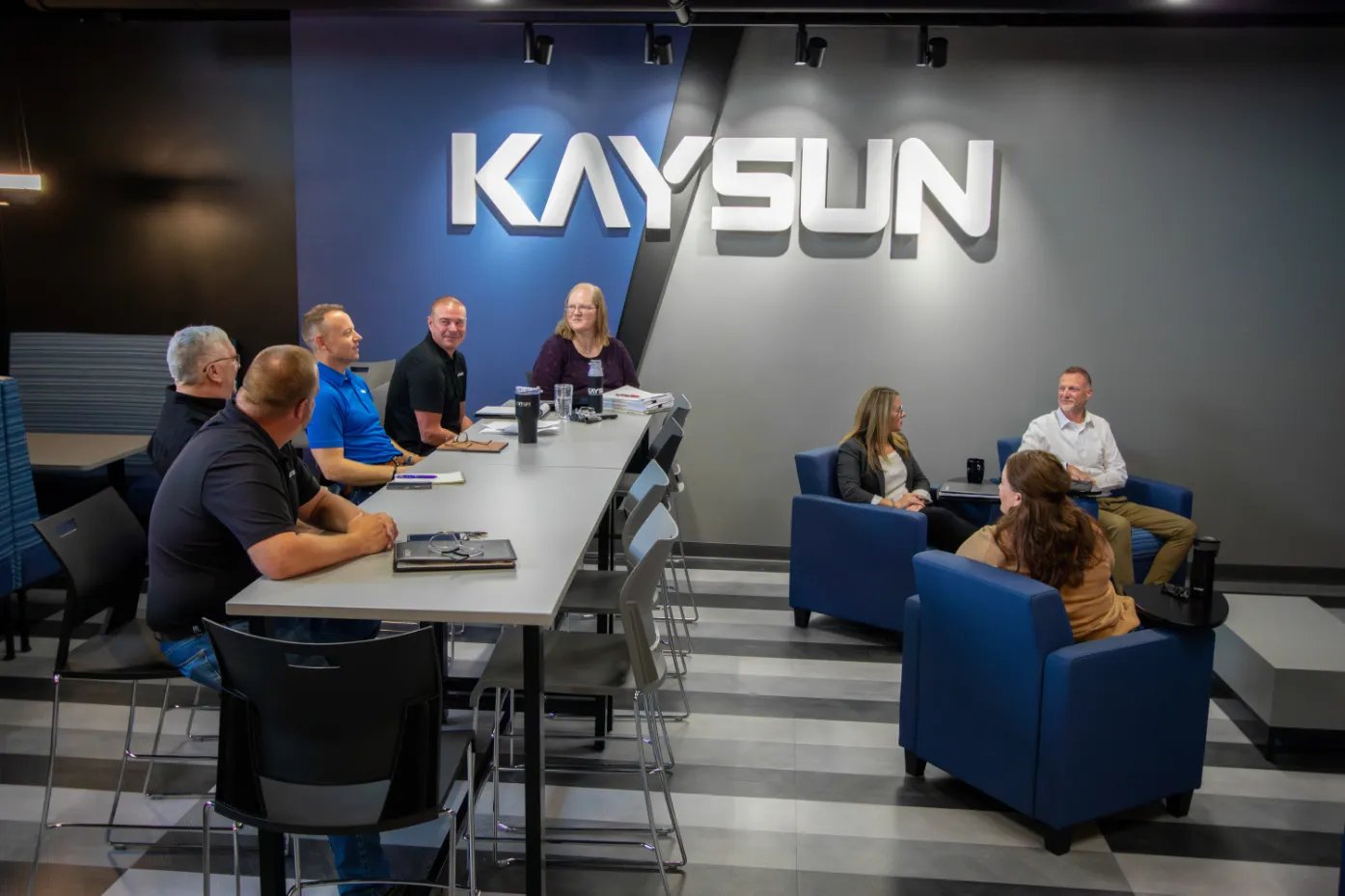
Does your company fit our ideal customer profile?
Complete the form to request a free consultation with our plastic engineering experts.